三菱ガス化学はこのほど、創立50周年の記念事業として、東京都江東区木場にイノベーションセンター「MGC Commons」を建設すると発表した。2023年10月の稼働開始を予定している。
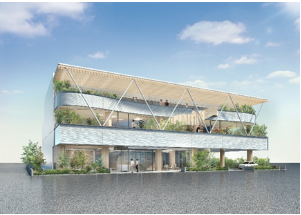
同社は、特色と存在感のある研究開発型企業として、数々のイノベーションを起こすことで成長し、2021年に創立50周年を迎えた。今後もさらに持続的に成長するため、企業理念「MGC Way」では、グループミッションに「社会と分かち合える価値の創造」を掲げている。
同センターでは、
2022年8月30日
2022年7月5日
2022年2月25日
2022年1月31日
2022年1月28日
LG化学はこのほど、超臨界水を利用した韓国初となる廃プラスチックの超臨界熱分解油施設を建設すると発表した。プラスチックの循環経済構築に向け、 “LG化学 プラスチックのケミカルリサイクル事業に参入” の続きを読む
2022年1月12日
循環型経済社会に貢献、23年度下期に稼働開始
大手ポリスチレン樹脂(PS)メーカー、東洋スチレン(デンカ50%、日鉄ケミカル&マテリアル35%、ダイセル15%)は11日、使用済みPSのケミカルリサイクル(CR)プラントを親会社であるデンカの千葉工場(千葉県市原市)の敷地内に建設すると発表した。投資金額は約38億円。年間処理能力は約3000tで、2023年度下期の稼働開始を予定している。
現在、SDGsの重要性が増大し、脱炭素・循環型社会構築の社会的要請が強まっている。プラスチックについても、
2021年12月15日
関西電力はこのほど、日本CCS調査(JCCS)と液化CO2出荷基地を同社舞鶴発電所構内に建設することに合意し、建設支援業務に係る委託契約を締結した。
CO2を回収し有効利用・貯留するCCUS技術は、ゼロカーボン社会実現の上で重要な技術の1つだが、CO2排出地と貯留・活用地は離れていることが多く、CO2を安全かつ低コストで輸送する技術の確立が課題である。
JCCSが代表するコンソーシアム(エンジニアリング協会、伊藤忠商事、日本製鉄)は、新エネルギー・産業技術総合開発機構(NEDO)の委託事業「CCUS研究開発・実証関連事業/苫小牧におけるCCUS大規模実証試験/CO2輸送に関する実証試験」に取り組んでいる。期間は今年度から6年間。
長距離・大量輸送に適したCO2の液化と貯蔵システム、輸送船舶の研究開発と設備機器の設計に伴う検討を行い、2023年度末頃を目途に年間1万t規模で舞鶴火力発電所から排出されるCO2を出荷基地で液化し、船舶輸送を経て苫小牧市の基地で受け入れる一貫輸送システムを運用し、操業に必要な技術を検証する。
そして、安全規格や設計基準の検討に必要な基礎要件を実証試験データから収集・分析し、液化CO2の長距離・大量輸送に求められる国際的なルールづくりにも取り組む。加えて、CO2輸送に関する実効性あるビジネスモデルの検討も進める。同社は、新たに建設する出荷基地の詳細設計に関する助言や、用地・施設・ユーティリティを提供し、CCUS技術の普及に向けた船舶によるCO2大量輸送技術の確立に貢献する考えだ。
2021年11月8日
ダウはこのほど、スコープ1、2のCO2排出に関して、世界初となる炭素排出量正味ゼロの統合型エチレンクラッカーおよび誘導体工場を建設すると発表した。
カナダのアルバータ州フォート・サスカチュワンに所在する既存設備を改修するとともに、エチレンおよびポリエチレン(PE)の生産能力を3倍に増強する。年間約10億ドル(またはD&A水準の3分の1)の設備投資を工場ごとに段階的に実施し、2030年までにエチレンクラッカーは約180万tの生産能力を追加。誘導品の生産能力や設備改修を通じて、低炭素またはゼロ炭素排出の認証を受けた約320万tのPEおよびエチレン誘導体を生産・供給できる見込みだ。
これにより、2030年までに、ダウの世界のエチレン生産能力約20%が脱炭素化される一方、PEの供給は約15%増加し、バリューチェーン全体で約10億ドルのEBITDA増大が見込まれる。
今回のプロジェクトは、同社のTX-9(米国テキサス州)投資に関する成功に基づいている。TX-9のクラッカーおよび誘導体装置と比較して、約15%低い資本集約度の実現が期待される。フォート・サスカチュワンの拠点を選択した理由として、炭素回収インフラの存在、競争力のある原料、政府との魅力的なパートナシップなどが挙げられる。
同社は、2050年までにカーボンニュートラルを達成することを目指し、2030年までに炭素排出量を約30%削減(2005年比)することを掲げている。今回のプロジェクトは、その取り組みを大きく推進すると見られる。
2021年10月25日
2021年8月30日
住友化学はこのほど、アクリル樹脂(PMMA、ポリメチルメタクリレート)のケミカルリサイクル(CR)実証設備を愛媛工場(愛媛県新居浜市)に建設すると発表した。2022年秋に実証試験に着手し、2023年にサンプル提供を開始する予定。この取り組みと並行して、使用済みアクリル樹脂の回収から、再生、製品化までの資源循環システムを確立し、早期の事業化を目指す。
アクリル樹脂は、合成樹脂の中でも極めて高い透明性をもつほか、耐候性や加工性にも優れ、自動車のテールランプカバーや家電、水槽、屋外看板、液晶ディスプレイ、建築材料、飛沫防止板などに幅広く使用されている。昨年の世界需要は130万tに上り、この先も堅調な伸びが予測されている。
同社は、環境意識の高まりを受け、自社での研究のほか、他企業やアカデミアとの協業により、様々なCRの技術開発を推進。アクリル樹脂については、日本製鋼所がもつ二軸混練押し出し機を利用したプラスチックの連続分解技術と、住友化学が長年培ってきたMMA(メチルメタクリレート)モノマーおよびアクリル樹脂の知見をもとに、同社と共同開発を進めてきた。
今回、アクリル樹脂を熱分解し、原料となるMMAモノマーとして再生する独自の基本技術を確立したことにより、実証設備の建設を決定した。この基本技術により得られたMMAモノマーを再重合してできるアクリル樹脂は、化石資源から製造したバージン材料と比較して、透明性や強度などの基本物性は同水準を維持した上で、製品ライフサイクル全体のGHG(温室効果ガス)排出量を60%以上削減できる見込みだ。
なお、今回の実証試験で原料とする使用済みアクリル樹脂は、水族館向け大型アクリルパネルで世界トップシェアを誇り、住友化学と約50年のパートナーである日プラから出る廃材を活用する予定。
また、事業化に向けて、廃棄される自動車や家電、飛沫防止板などからの回収を含め、安定的な原料調達システムの構築も併せて検討を始める。再生MMAモノマー、およびそれを原料とするアクリル樹脂は、環境規制の強化が進む自動車のほか、公共施設である高速道路の遮音板など、リサイクル材料としての付加価値が認められる分野・製品での採用を想定している。