大陽日酸はこのほど、高圧ガスを安全に利用してもらうための保安力向上サービス「みんなガスシル」の提供を開始した。
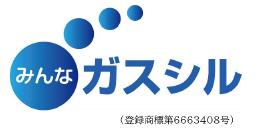
高圧ガスの法規制は
2023年4月19日
2023年4月17日
2023年3月2日
2023年2月14日
2023年1月24日
[大陽日酸・人事](3月31日)▽退任(常務執行役員工業ガスユニット長兼ガス事業部長兼基盤事業支援ユニット長)栗下敏一※4月1日付大陽日酸エネルギー顧問就任・六月総会日付同社社長就任▽同(同役員プラントエンジニアリングセンター長)佐藤豊幸※4月1日付ティーエムエアー顧問就任・六月総会日付同社社長就任▽同(同役員電子機材ユニット長兼電子機材ガス事業部長兼基盤事業支援ユニット副ユニット長)高木正治※4月1日付サーンエンジニアリング社長就任▽同(執行役員生産・物流ユニット長)中島太司※4月1日付千葉サンソセンター顧問就任・五月総会日付同社社長就任▽退任(同役員東北支社長)日向野正行※4月1日付ジャパンヘリウムセンター顧問就任・六月総会日付同社社長就任(4月1日)▽常務執行役員イノベーションユニット長小林邦裕▽同役員電子機材ユニット長兼基盤事業支援ユニット長相田智之▽同役員工業ガスユニット長兼基盤事業支援ユニット副ユニット長飯塚浩幸▽執行役員プラントエンジニアリングセンター長柳川徹▽同役員技術開発ユニット長武内雅弘▽同役員中部支社長竹内聡一郎▽同役員メディカルユニット長古海敏恵▽同役員九州支社長古賀公貴▽理事オンサイト・プラントユニット長兼オンサイト事業部長千田健一郎▽同生産・物流ユニット長宇杉晃一▽同同ユニット副ユニット長兼技術統括部長内城保▽同ガスエンジニアリングセンター長原田裕司▽同経営企画・ICTユニット長丹羽善之▽同東北支社長吉田秀【大陽日酸JFP】(4月1日)▽顧問(出向)渡邉忠治※六月総会日付社長(出向)就任▽退任(社長)、顧問河野靖彦【大陽日酸エネルギー】(6月総会日)▽退任(社長)、顧問神﨑昌久。
2023年1月23日
2023年1月20日
2022年12月14日
日本液炭はこのほど、液化炭酸ガスおよびドライアイスについて2023年2月出荷分から値上げすると発表した。改定幅はいずれも「20%以上」。
同社はエネルギー市況高騰による電力料金の上昇や鋼材価格・各種原材料費の高騰、また原料を依存する製油所などの事業縮小による調達量減少を補完するためのコスト上昇に伴い、今年2月出荷分から「平均15%程度」の価格改定を進めてきた。
しかし、それ以降も電力料金は大幅に上昇し続けており、足元のエネルギー市況・為替動向や脱炭素の潮流からも、製造に係わるユーティリティーコストは当分高止まりすることが想定される。
また、原料ひっ迫による長距離輸送の増加や物流人件費の上昇など、安定供給のためのコストは、著しい上昇を続けている。こうした中、同社は、上昇コストの吸収は企業努力の範囲を大きく超え、従来価格の維持が困難なものとなっていることから、高品質な製品を継続的に安定供給するために、今回、改めて価格改定を決定した。
2022年12月13日
2022年11月22日